Understanding the importance of proper electrical labeling
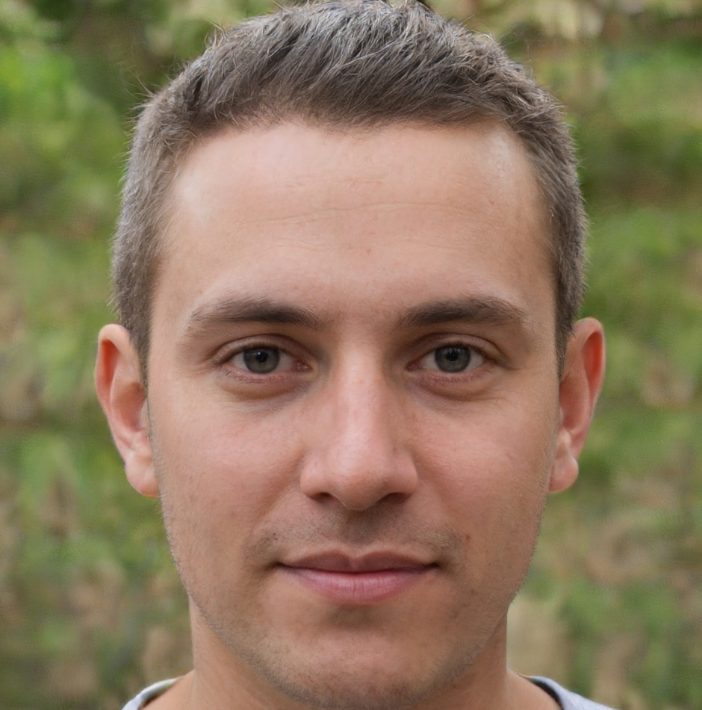

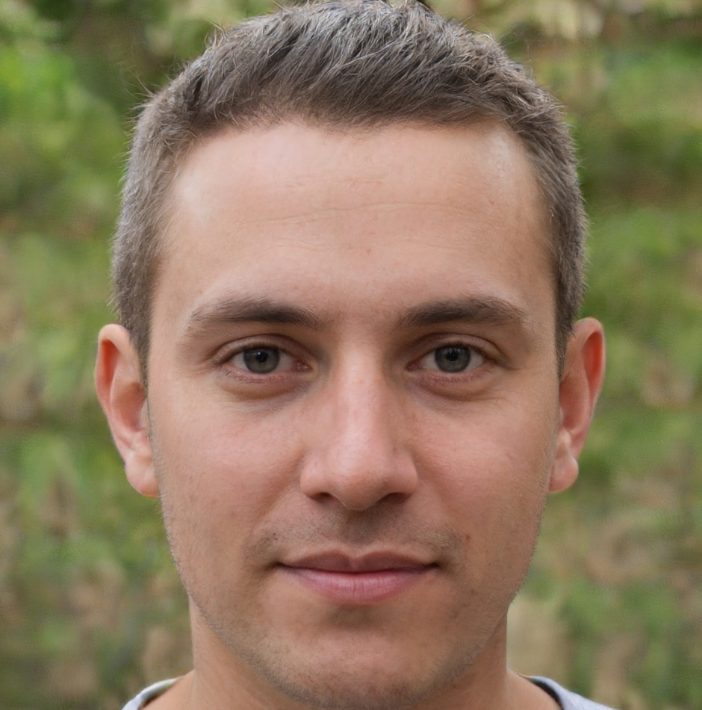
Understanding the Importance of Proper Electrical Labeling
Electrical systems are the backbone of our daily lives, powering everything from our homes to our workplaces. However, with great power comes great responsibility, and ensuring the safety and efficiency of electrical systems requires careful planning, installation, and maintenance. One crucial aspect of electrical system management is proper electrical labeling. In this article, we'll delve into the importance of proper electrical labeling, its benefits, and the potential consequences of inadequate labeling.
Proper Electrical Labeling: A Safety Imperative
Electrical labeling is a critical component of electrical system management, serving as a visual identification system that enables workers, inspectors, and emergency responders to quickly identify electrical components, circuits, and systems. Proper labeling provides essential information about the electrical system, including voltage, current, and hazard warnings. This information is vital for ensuring the safety of individuals working on or around electrical systems.
Inadequate labeling can lead to catastrophic consequences, including electrical shocks, fires, and even fatalities. According to the Occupational Safety and Health Administration (OSHA), electrical hazards are a leading cause of workplace accidents, resulting in over 4,000 injuries and 300 deaths annually in the United States alone. Proper electrical labeling can significantly reduce the risk of these accidents by providing clear and concise information about the electrical system.
Benefits of Proper Electrical Labeling
Proper electrical labeling offers numerous benefits, including:
Improved Safety
Proper labeling ensures that workers and emergency responders can quickly identify electrical components and systems, reducing the risk of electrical shocks, fires, and other hazards.
Enhanced Efficiency
Clear and concise labeling enables workers to quickly locate and identify electrical components, reducing the time spent on maintenance, repairs, and troubleshooting.
Reduced Downtime
Proper labeling helps minimize downtime by ensuring that electrical systems can be quickly restored to operation after an outage or failure.
Compliance with Regulations
Proper electrical labeling is essential for compliance with electrical safety codes and regulations, such as the National Electric Code (NEC) and OSHA standards.
Extended Equipment Life
Proper labeling helps ensure that electrical equipment is properly installed, maintained, and repaired, extending its lifespan and reducing maintenance costs.
Consequences of Inadequate Labeling
The consequences of inadequate electrical labeling can be severe and far-reaching, including:
Electrical Shocks and Injuries
Inadequate labeling can lead to electrical shocks, injuries, and even fatalities, particularly when workers are unsure of the electrical system's configuration or voltage levels.
Equipment Damage and Failure
Inadequate labeling can result in equipment damage, failure, and premature wear, leading to costly repairs, replacements, and downtime.
Fire Hazards
Inadequate labeling can increase the risk of electrical fires, which can spread quickly and cause significant damage to property and infrastructure.
Compliance Issues
Inadequate labeling can result in non-compliance with electrical safety codes and regulations, leading to fines, penalties, and legal liability.
Increased Maintenance Costs
Inadequate labeling can lead to increased maintenance costs, as workers may need to spend more time locating and identifying electrical components.
Real-World Examples of Effective Electrical Labeling
Several industries and organizations have implemented effective electrical labeling systems, including:
Data Centers
Data centers, which rely on high-capacity electrical systems to power IT infrastructure, use comprehensive labeling systems to ensure rapid identification of electrical components and systems.
Industrial Facilities
Industrial facilities, such as manufacturing plants and oil refineries, use electrical labeling to ensure worker safety and minimize downtime.
Healthcare Facilities
Healthcare facilities, where electrical systems are critical to patient care, use electrical labeling to ensure rapid identification of electrical components and systems.
Case Study: The Importance of Proper Labeling in Industrial Settings
A manufacturing plant in the Midwest experienced a series of electrical accidents, resulting in injuries and fatalities. An investigation revealed that the lack of proper labeling was a primary cause of the accidents. The plant's electrical system was complex, with multiple circuits and devices, but there were no labels to identify the voltage, amperage, or other critical information.
As a result, electricians and maintenance personnel were unsure of how to safely repair and maintain the electrical system. The plant implemented a comprehensive labeling program, which included standardizing labels, using clear and concise language, and labeling all electrical components.
The results were significant. The number of electrical accidents decreased by 75%, and downtime was reduced by 50%. The plant's maintenance personnel reported a significant improvement in their ability to quickly identify and repair faults, reducing the time spent on repairs and increasing productivity.
Best Practices for Electrical Labeling
To ensure proper electrical labeling, follow these best practices:
Use Clear and Concise Labels
Use clear, concise, and easily readable labels that provide essential information about the electrical system.
Follow Industry Standards
Follow industry standards, such as the NEC and OSHA guidelines, for electrical labeling.
Use Durable Labels
Use durable labels that can withstand environmental factors, such as temperature, humidity, and exposure to chemicals.
Label All Electrical Components
Label all electrical components, including circuit breakers, fuses, and electrical panels.
Regularly Inspect and Update Labels
Regularly inspect and update labels to ensure they remain accurate and up-to-date.
Conclusion
Proper electrical labeling is a critical aspect of electrical system management, ensuring the safety and efficiency of electrical systems. Inadequate labeling can lead to catastrophic consequences, including electrical shocks, fires, and fatalities. By following best practices and industry standards, organizations can ensure proper electrical labeling, reduce the risk of accidents, and ensure compliance with electrical safety codes and regulations. Remember, proper electrical labeling is not just a recommandation – it's a necessity for ensuring the safety and reliablility of electrical systems.
In conclusion, the importance of proper electrical labeling cannot be overstated. It's a critical component of electrical system management that ensures the safety and efficiency of electrical systems. By following best practices and industry standards, organizations can reduce the risk of electrical accidents, ensure compliance with regulations, and minimize downtime. So, don't wait – prioritize electrical labeling today and ensure the safety and reliability of your electrical systems.